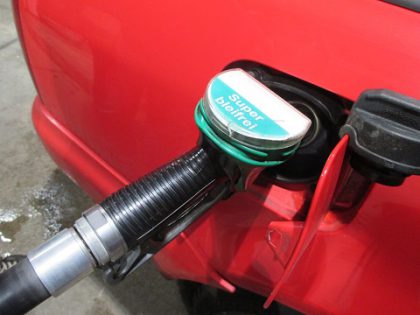
Optimal combination of two devices ensures faster hardening of the moulded plastic component and shortens cooling time by 60%. This is what the media press of “ABOPR” of Germany has released for PIMI Channel. New innovation for the auto industry.
When manufacturing fuel tanks for the automotive industry, the multi-layer or co-extrusion process “COEX” is mostly used these days: A tubular preform made of molten polymers – virgin HDPE, HDPE regranulate, an internal and external bonding layer, EVOH and again virgin HDPE – is transferred into a blow mould and adjusted to mould contours due to interior pressure. In order to cure the tank, it has so far been cooled only by means of cold water in the cavity of the tool mould. However, the process step was very cost-intensive and time-consuming, because low cold water temperature led to formation of condensation on the mould surface, which in turn resulted in unsteady product quality and increased scrap. Moreover, due to the continuing heat exposure, the EVOH-layer in the tank was damaged and thus the functional capability limited. This is where the Mould Area Protection (MAP) system of FarragTech GmbH comes in: Due to the supply of dry air, the mould is prevented from sweating. For further increase of output, the Internal Air Cooling System (IACS) from FarragTech is also suitable: During the process, in addition to conventional cooling, the tank is internally flushed with -35 °C cold air, whereby heat in the plastic is simultaneously taken away inside and outside, with material stress being prevented. Thus during production, time and money can be effectively saved.
“Cooling of the plastic product represents both one of the most critical and most lengthy sub-processes in the extrusion blow moulding process,” explains Aaron Farrag, deputy CEO of the FarragTech GmbH. “Especially during production of multi-layer products such as modern fuel tanks, a lot of time can be saved and the EVOH-layer protected against damages due to heat exposure.” During the process, difficulties can occur due to the temperature drop between the exterior cooled by means of cold water and the still warm interior of the product. These temperature differences so far often led to significant material stress – above all, because the large-scale tanks are complexly shaped, showing so different wall thicknesses in the range of 1.35 mm and 3.80 mm. Until recently, this was counteracted by means of interval blowing. But this process was less effective. As a rule, the results were unsteady product quality as well as failure to pass the subsequently carried out tightness tests, load tests as well as drop tests. By reason of the relatively high scrap rate, the costs of production increased.
To read the full document and for more information, please refer to: “farragtech.com“.
************************
Why Should Be “A Paid-Subscriber” and “Advertiser”
Keeping an independent media in countries that impose limitations on self supporting media, will help to support the humankind’s freedom. If you believe it, please act to be a PRO-MEMBER by clicking “HERE“, or:
Please send your PR’s directly to the email address of the Chief-Editor in order to be published at once in the world via ” http://pimi.ir ” The address is: aasaatnia@live.com.