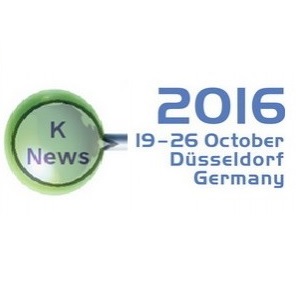
3D-printed sacrificial tooling, or more specifically 3D-printed molds and mandrels, can enable manufacturers to rapidly and cost-effectively create complex composite parts with geometries that would normally trap the tool.
To further improve the process, 3D-technology provider Stratasys (Eden Prairie, MN) has introduced an innovative sacrificial tooling solution. It features Stratasys’ new ST-130 material based on Ultem 1010 polyetherimide (PEI) from Sabic Innovative Plastics along with alternative fill patterns (patent pending) designed for faster dissolution, rapid build speed, and greatly improved tool quality and autoclave performance. The new ST-130 material is available for the Stratasys Fortus 450mc and 900mc Production 3D Printers.
3D-printed sacrificial tooling, or more specifically 3D-printed molds and mandrels, can enable manufacturers to rapidly and cost-effectively create complex composite parts with geometries that would normally trap the tool.
To further improve the process, 3D-technology provider Stratasys (Eden Prairie, MN) has introduced an innovative sacrificial tooling solution. It features Stratasys’ new ST-130 material based on Ultem 1010 polyetherimide (PEI) from Sabic Innovative Plastics along with alternative fill patterns (patent pending) designed for faster dissolution, rapid build speed, and greatly improved tool quality and autoclave performance. The new ST-130 material is available for the Stratasys Fortus 450mc and 900mc Production 3D Printers.
Traditional manufacturing methods for high-performance, polymer matrix composite structures require the use of hard tooling for the mold or mandrel that dictates the final part shape. Whether made from metal or specialty non-metallic materials, fabricating this tooling requires significant labor and machining resources – leading to high costs, waste, and long lead times sometimes stretching into many months for more complex tools.
In contrast, Stratasys 3D printed composite tooling using Ultem 1010 enables manufacturers to produce high temperature (>350°F), autoclave-cured composite structures in a fraction of the time need for traditional tooling, while also achieving cost savings. “Stratasys produced composite tools allows us to develop the same types of products much faster without compromising quality or performance of the part,” said Rick Heise, President, Swift Engineering.
At SAMPE 2016 (May 23–26, Long Beach, CA), Stratasys hosted representatives from Dassault Falcon Jet at the Stratasys booth to showcase and display their Stratasys 3D printed tooling design solutions.
Stratasys also launched a comprehensive Design Guide at SAMPE that provides essential data and guidance for 3D printed composite tooling. Tim Schniepp, Composite Tooling Director, Stratasys will present an overview of the Guide at SAMPE with a technical paper entitled “Design Guide Development for Additive Manufacturing of Composite Tooling” on Thursday, May 26 at 10am, room 102 B.
“We developed the Design Guide to provide our customers with the ability to immediately realize the time and cost-saving benefits of FDM-based 3D printed composite tooling without the effort and expense required to develop the knowledge independently. This allows Stratasys users to better leverage their time and resources in addressing their manufacturing challenges,” said Tim Schniepp, Composite Tooling Director at Stratasys.
Producing the large composite parts and associated tooling typically used in aerospace, automotive and other demanding applications can take several weeks to many months for fabrication. To reduce production time and costs, Stratasys has developed the Fortus 900mc Acceleration Kit. This new solution allows very large tools to be produced up to three times faster in ASA and ULTEM 1010 materials.
Release Date: 06/06/2016