“EREMA Recycles 30 Tons of Plastic Waste Live at K 2016”
On October 19, the CAREFORMANCE Recycling Center was opened at the Düsseldorf fairground, ready to process over 30 tons of plastic waste accumulated during K 2016.
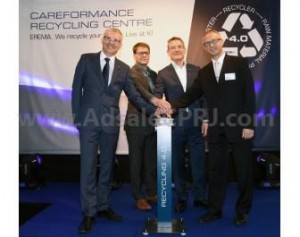
Manfred Hackl of EREMA, Alfred Stern of Borealis, Ton Emans of PRE and Alexandre Dangis of EuPC all pressed the buzzer together for the grand opening.
“The collaboration of the entire ‘plastic’ value chain has become more intensive in recent years and results in terms of product innovations – particularly in the case of recycling projects – deserve a special platform at K,” emphasized Hackl, CEO of EREMA.
Plastic wastes are recycled live on an INTAREMA TVEplus 1108 recycling system, which is the first Industry 4.0 packaging in the field of plastics recycling.
“EREMA has developed a Smart Factory package for producers and recyclers. On the one hand, the process data of the individual machines is analyzed and, on the other, the production and recycling facilities are interconnected with the entire process chain,” Hackl explained.
The machine, quality and process data of the recycling process in the CAREFORMANCE Recycling Center are relayed in real time directly to EREMA’s booth. Hackl is confident that this digital quality proof will further increase the amount of recyclate used in the production of plastics.
Along with the CAREFORMANCE Recycling Center, Borealis, Hosokawa Alpine, Bobst, GEA and EREMA presented the latest developments in the production of recyclable stand-up pouches.
This collaboration makes possible for the first time to produce pouches with a material combination based exclusively on polyethylene (PE).
The companies involved demonstrate impressively how the closed plastic loop works: the pouches produced on site – including any production waste – are likewise recycled live and the recyclates processed directly on an OCS extruder to make blown film.
“I like to compare the plastic loop to a relay race. It is not enough if a part of the value chain thinks only in terms of their processing step. Every manufacturer or processor of plastics has to think one step further to reach the finish line successfully together,” said Hackl.