3D printing and MR fluid infilling of unit cells. (A) Schematic illustration of the LAPμSL 3D printing process used to build struts, unit cells, and lattices. (B) Optical image of a resin-filled polymer cuboctahedron unit cell. (C) Optical image of drained (hollow) unit cells affixed with a dissolvable wax to syringe nozzles for infilling. (D) Optical images from a time-lapse recording of the MR fluid filling in process. (E to G) Optical image of the unit cell with inlet (green) and outlet (red) ports separated by various strut lengths. (E) Ports separated by one strut. (F) Ports separated by two struts. (G) Ports separated by three struts with the highest degree of infilling. Credit: Science Advances, doi: 10.1126/sciadv.aau6419.
properties are programmed and set when the architecture is designed and constructed, and do not change in response to shifting environmental conditions or application requirements. In a recent study published in Science Advances, materials scientists Julie A. Jackson and colleagues presented a new class of materials architecture called field-responsive mechanical metamaterials (FRMM).
The FRMMs exhibit dynamic control and on-the-fly tunability for designing and selecting the construct’s composition and structure. Typically, properties of mechanical metamaterials are programmed and set when the architecture is designed and constructed, without changing in response to shifting external environmental conditions or applications thereafter. The diverse characteristics of FRMMs were first demonstrated by printing complex structures of polymeric tubes filled in with magnetorheological (MR) fluid suspensions to allow remote magnetic fields to control the materials. Accordingly, the scientists observed rapid, reversible and sizable changes of the effective stiffness in the new metamaterial constructs.
Synthetic materials often mimic cellular structures such as teeth, bone and bird beaks in nature to replicate their excellent strength and toughness relative to density. Advanced materials are bioengineered to mimic stochastic (random) cellular structures in the form of polymers and metal foams for structural and functional applications. Nature can also create periodic architectures by evolutionary design, where ordered cellular structures outperform the stochastic counterparts as seen with defensive armor shells and dactyl clubs in crustacea.
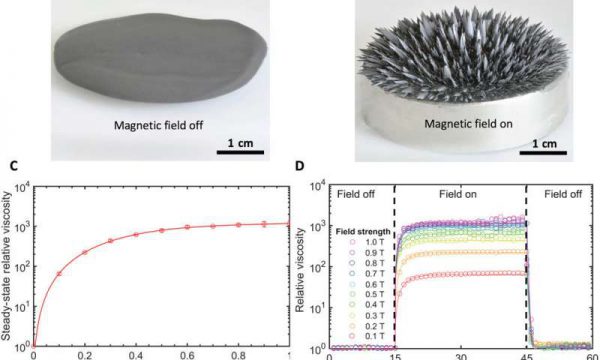
In the lab, additive manufacturing techniques and 3-D printing are used to engineer cellular structures with nano-, micro-, meso- and macro-scale features that exhibit unique combinations of mechanical, functional and thermal properties. Often referred to as metamaterials, the structures have demonstrated innovative characteristics, including: * Lightweight, yet stiff and strong architecture in 3-D ceramic nanolattices * High mechanical resilience in graphene periodic 3-D aerogel microlattices. * Negative Poisson’s ratio in origami-based metamaterials. * Elasto-mechanical “unfeelability” cloaks and invisibility cloaks * Multimaterial layouts with negative coefficients of thermal expansion.
*
These materials combine two or more contrasting features for unique properties, but their architecture remains fixed in time after fabrication. As a result, the materials cannot respond and adapt to changing external conditions. Adaptable and responsive materials are increasingly engineered via 4-D printing,
For more information check “SOURCE”
************************
Why Should Be “A Paid-Subscriber” and “Advertiser”
Keeping an independent media in countries that impose limitations on self supporting media, will help to support the humankind’s freedom. If you believe it, please act to be a PRO-MEMBER by clicking “HERE“, or:
Please send your PR’s directly to the email address of the Chief-Editor in order to be published at once in the world via ” http://pimi.ir ” The address is: aasaatnia@live.com