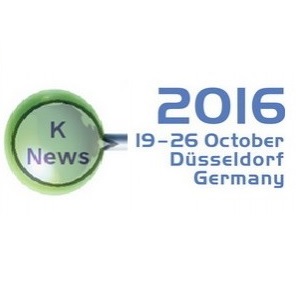
Tolerances: Are you hitting the target or the bull’s-eye?
06/03/2016
“Why will only being within tolerance make a good part?” the consultant asked.
A good analogy is target shooting. Hitting the target gets you points; missing it gets you nothing. Specifying a target that’s too small to hit ruins the competition, because now it’s down to sheer luck and not accuracy!
Consider the concepts of Cp and CpK, which originated in the precision machining business. Cp looks strictly at process variation. In the machining business, if your drill wobbles in the press, the accuracy and precision of the hole will be no better than the amount of wobble. Going back to our analogy, Cp defines the size of the target. CpK looks at how much you varied from the specified dimension (the bull’s-eye). This was developed in the machine tool industry, because the equipment running the cutting tool only knows the dead center of the cutter, but the size of the hole is where the cutting teeth are. CpK was the tool developed to look at the wear of the cutter.
A CpK of 1.0 means the entire target. But a CpK of 1.3 has essentially cut the target size by 50%! In plastics terms, if the tolerance is ±0.002, the designer has essentially required you to hold ±0.001.
Going back to our analogy: If your shots are all over the target, you’ve just defined your CP (assuming a stable process). If you have a tight group of shots in the upper right hand corner of the target, the precision of your shooting is very repeatable; with a little tweaking of your sites, style or something else, you can move this tight group into the bull’s-eye, thereby improving your CpK of target shooting.
Now, let’s look at the real world, and switch analogies. When an area has a spring flood, there’s always a lively debate that boils down to raising the dam or lowering the water. Raising the dam is a massive capital expense for which nobody wants to pay. Lowering the water means you create the flood earlier on in the hope that the real flood can be contained.
In terms of design requirements, raising the dam equates to buying/refurbishing equipment with the expectation that the newly acquired precision will meet the requirements of the design. Buyers routinely make these demands of their customers because they don’t care what it costs them.
Lowering the water is where I come in. It’s a wonderful debate when I ask the designer: “Explain to me . . . ” usually in the context of why his specified ±0.0005-inch tolerance is the difference between a successful product and either shortened product life or a catastrophic product failure.
It’s interesting to have this discussion. When I ask: “What happens if the part is ±0.002 inches? Will it still assemble? Will it fail?” More importantly, “perhaps we should be looking at CNC machining as either a secondary operation or replacing injection molding altogether and machine this part.” This is really a design for manufacturing (DFM) discussion. DFM says you design it to be made, not simply designed.