The following article which has originally been published on phys.org is chosen for our interested readers to PET recycling. However, in order to add more value to it, several hyperlinks (shown in BOLD fonts) and selective related images has been added to the article plus minor editing needs. The main page image belongs to the Green Chemistry Journal.
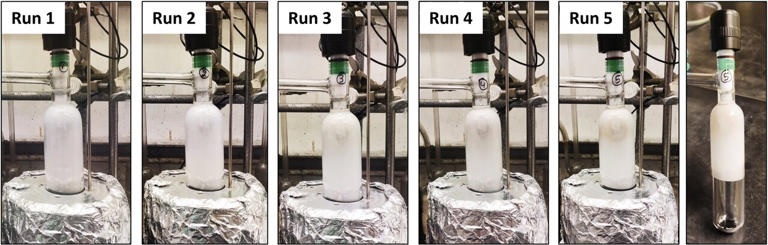
The non-toxic, environmentally friendly, solvent-free process first uses an inexpensive catalyst to break apart the bonds in polyethylene terephthalate (PET), the most common plastic in the polyester family. Then, the researchers merely expose the broken pieces to ambient air. Leveraging the trace amounts of moisture in air, the broken-down PET is converted into monomers—the crucial building blocks for plastics. From there, the researchers envision the monomers could be recycled into new PET products or other, more valuable materials.
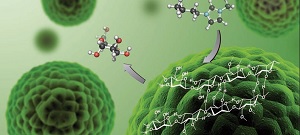
Safer, cleaner, cheaper and more sustainable than current plastic recycling methods, the new technique offers a promising path toward creating a circular economy for plastics. The study was recently published in Green Chemistry.
“The U.S. is the number one plastic polluter per capita, and we only recycle 5% of those plastics,” said Northwestern’s Yosi Kratish, the study’s co-corresponding author. “There is a dire need for better technologies that can process different types of plastic waste. Most of the technologies that we have today melt down plastic bottles and downcycle them into lower-quality products.
“What’s particularly exciting about our research is that we harnessed moisture from air to break down the plastics, achieving an exceptionally clean and selective process. By recovering the monomers, which are the basic building blocks of PET, we can recycle or even upcycle them into more valuable materials.”
“Our study offers a sustainable and efficient solution to one of the world’s most pressing environmental challenges: plastic waste,” said Naveen Malik, the study’s first author. “Unlike traditional recycling methods, which often produce harmful byproducts like waste salts and require significant energy or chemical inputs, our approach uses a solvent-free process that relies on trace moisture from ambient air. This makes it not only environmentally friendly but also highly practical for real-world applications.”
An expert in plastic recycling, Kratish is a research assistant professor of chemistry at Northwestern’s Weinberg College of Arts and Sciences. Kratish co-led the study with Tobin J. Marks, the Charles E. and Emma H. Morrison Professor of Chemistry at Weinberg and a professor of materials science and engineering at Northwestern’s McCormick School of Engineering. At the time of the research, Malik was a postdoctoral fellow in Marks’ laboratory; now he is a research assistant professor at the SRM Institute of Science and Technology in India.
The plastic problem
Commonly used in food packaging and beverage bottles, PET plastics represent 12% of total plastics used globally. Because it does not break down easily, PET is a major contributor to plastic pollution. After use, it either ends up in landfills or, over time, degrades into tiny microplastics or nanoplastics, which often end up in wastewater and waterways.
Finding new ways to recycle plastic is a hot topic in research. But current methods to break down plastics require harsh conditions, including extremely high temperatures, intense energy and solvents, which generate toxic byproducts. The catalysts used in these reactions are also often expensive (like platinum and palladium) or toxic, creating even more harmful waste. Then, after the reaction is performed, researchers have to separate the recycled materials from the solvents, which can be a time-consuming and energy-intensive process.
In previous work, Marks’ group at Northwestern became the first to develop catalytic processes that do not require solvents. In the new study, the team again devised a solvent-free process.
“Using solvents has many disadvantages,” Kratish said. “They can be expensive, and you have to heat them up to high temperatures. Then, after the reaction, you are left with a soup of materials that you have to sort to recover the monomers. Instead of using solvents, we used water vapor from air. It’s a much more elegant way to tackle plastic recycling issues.”
An ‘elegant’ solution
To conduct the new study, the researchers used a molybdenum catalyst and activated carbon—both of which are inexpensive, abundant and non-toxic materials. To initiate the process, the researchers added PET to the catalyst and activated carbon and then heated up the mixture. Polyester plastics are large molecules with repeating units, which are linked together with chemical bonds. After a short period of time, the chemical bonds within the plastic broke apart.
Next, the researchers exposed the material to air. With the tiny bit of moisture from air, the material turned into terephthalic acid (TPA)—the highly valuable precursor to polyesters. The only byproduct was acetaldehyde, a valuable, easy-to-remove industrial chemical.
“Air contains a significant amount of moisture, making it a readily available and sustainable resource for chemical reactions,” Malik said. “On average, even in relatively dry conditions, the atmosphere holds about 10,000 to15,000 cubic kilometers of water. Leveraging air moisture allows us to eliminate bulk solvents, reduce energy input and avoid the use of aggressive chemicals, making the process cleaner and more environmentally friendly.”
“It worked perfectly,” Kratish said. “When we added extra water, it stopped working because it was too much water. It’s a fine balance. But it turns out the amount of water in air was just the right amount.”
Endless advantages
The resulting process is fast and effective. In just four hours, 94% of the possible TPA was recovered. The catalyst is also durable and recyclable, meaning it can be used time and time again without losing effectiveness. And the method works with mixed plastics, selectively recycling only polyesters. With its selective nature, the process bypasses the need to sort the plastics before applying the catalyst—a major economic advantage for the recycling industry.
When the team tested the process on real-world materials like plastic bottles, shirts and mixed plastic waste, it proved just as effective. It even broke down colored plastics into pure, colorless TPA.
Next, the researchers plan to increase the scale of the process for industrial use. By optimizing the process for large-scale applications, the researchers aim to ensure it can handle vast quantities of plastic waste.
“Our technology has the potential to significantly reduce plastic pollution, lower the environmental footprint of plastics and contribute to a circular economy where materials are reused rather than discarded,” Malik said. “It’s a tangible step toward a cleaner, greener future, and it demonstrates how innovative chemistry can address global challenges in a way that aligns with nature.”
More information: Naveen Malik et al, Thermodynamically leveraged solventless aerobic deconstruction of polyethylene-terephthalate plastics over a single-site molybdenum-dioxo catalyst, Green Chemistry (2025). DOI: 10.1039/D4GC05916F
Provided by Northwestern University