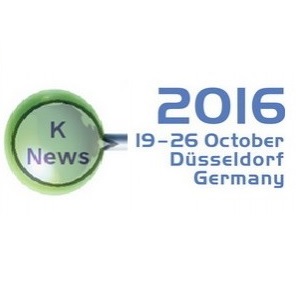
Oak Ridge Licenses Carbon Fiber Production Technology
RMX Technologies (Knoxville, TN) and the Department of Energy’s Oak Ridge National Laboratory have signed an exclusive licensing agreement for a new technology that dramatically reduces the time and energy needed in the production of carbon fiber.
The ORNL/RMX plasma processing technology is a new approach to the oxidation stage of carbon fiber production in which polymer materials are oxidized (or stabilized) before carbonization. During oxidation, the thermoplastic precursor is converted to a thermoset material that can no longer be melted. Oxidation is the most time-consuming phase of the multistep carbon fiber conversion process.
RMX Technologies (Knoxville, TN) and the Department of Energy’s Oak Ridge National Laboratory have signed an exclusive licensing agreement for a new technology that dramatically reduces the time and energy needed in the production of carbon fiber.
![]() |
Plasma oxidation oven is key to the low-cost, rapid process for carbon fiber production. |
The ORNL/RMX plasma processing technology is a new approach to the oxidation stage of carbon fiber production in which polymer materials are oxidized (or stabilized) before carbonization. During oxidation, the thermoplastic precursor is converted to a thermoset material that can no longer be melted. Oxidation is the most time-consuming phase of the multistep carbon fiber conversion process.
“In conventional systems, it generally takes between 80 and 120 minutes for oxidation,” said ORNL co-inventor Felix Paulauskas. “We found a way to cut the time by a factor of 2.5 to 3 times, so we can process fiber in 25 to 35 minutes.”
Compared to conventional oxidation techniques, the team’s plasma oxidation technology reduces unit energy consumption by 75 percent and lowers production costs by 20 percent, while maintaining or improving the resulting carbon fiber quality. Plasma oxidation can be used to produce all grades of carbon fiber from low-end industrial to high-end aerospace grades.
Paulauskas developed the scientific concept for the plasma oxidation method eight years ago and worked with RMX Technologies to develop prototypes and demonstrate the technology at the lab scale. In 2014, RMX constructed a 1-ton plasma oxidation oven at its facility and transitioned from development to scaling and commercialization the following year.
“We are commercializing this technology with our industrial partners to manufacture low-cost carbon fiber and create quality jobs,” RMX Technologies president Rodney Grubb said. “Through our partnership with ORNL, we have proven 75-percent energy savings, we make a quality fiber, and the equipment uses less than half the space. One of our carbon fiber production partners told us, ‘Plasma oxidation is not a science project anymore. The technology works.’”
Grubb said the company is preparing quotes with its commercial partner, C.A. Litzler, a manufacturer of carbon fiber production equipment, and expects to sell its first plasma oxidation oven in 2017. An RMX subsidiary, 4M Industrial Oxidation, will jointly manufacture and license the technology with Litzler.
“Commercialization of this technology can accelerate the use of carbon fiber in the auto industry and expand into other areas where strong and lightweight materials provide benefits,” said Truman Bonds, RMX Technologies vice president for research and development.
The Department of Energy’s (DOE) Vehicle Technologies Office has funded ORNL’s research in plasma oxidation of carbon fiber. ORNL is managed by UT-Battelle for the DOE’s Office of Science, the single largest supporter of basic research in the physical sciences in the United States.