The following article has been chosen from the CHINAPLAS 2025 website, and for the good sake of our readers has been more informative by addition of several hyperlinks.
**********************************************
“The Top Ten Technology Trends in Plastics and Rubber in 2025” campaign initiated by Adsale Plastics Network has been gaining momentum, with nearly 120 new products and technologies submitted by leading global suppliers. Over 2,700 readers participated in the voting, and 20+ industry experts are conducting evaluations based on the criteria including technological breakthrough and industrial impact.
To showcase the innovative advancements in materials and processing, we will introduce many of the technologies submitted in detail. Today we spotlight the most actively submitted category: Lightweighting, Modified Materials and Additives. The 20+ submitted products and technologies demonstrate six core advancements:
∎ High-strength lightweighting
∎ High-toughness lightweighting
∎ Enhanced skin-friendly surface properties
∎ Halogen-free, fluoride-free flame retardant modification
∎ Diversified low-carbon manufacturing solutions
∎ Efficiency-driven automation and microcellular foam molding
High-strength lightweighting
From low-altitude vehicles and hydrogen-powered cars to humanoid robots – these emerging technologies defining the future of mobility and industrial manufacturing demand materials that not only achieve lightweight and high-strength properties but must also withstand complex operational environments.
Products and technologies from Kingfa, Victrex, Arkema, WOTE and KUMHO-SUNNY demonstrate how breakthroughs in molecular structure optimization and production process refinement enable the critical balance between weight reduction and structural integrity, while ensuring performance in harsh scenarios involving extreme temperatures, friction and mechanical stress.
∎ Kingfa Sci.&Tech.
Technology: High-Strength Continuous Fiber-Reinforced Polyamide
Applications: Robotic
Kingfa has independently developed its Premium-Grade Continuous Fiber-Reinforced Polyamide (LFT-PA) – an integrated material that leverages 30% + density reduction and corrosion resistance to enable robotic skeletons to achieve both agile motion and long-term durability in dynamic loading scenarios.
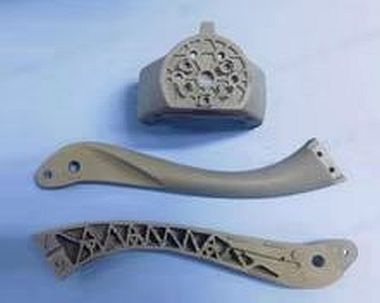
The material utilizes the company’s proprietary fiber impregnation and preheating technologies, ensuring flawless particle appearance and uniform performance consistency. Through advanced formula engineering, it delivers high-strength mechanical properties (tensile strength ≥250MPa; flexural modulus 15,000MPa) while achieving color diversity and high-gloss finish — fulfilling the dual requirements of performance and aesthetics for robotic structural components.
Victrex
Technology: LMPAEK™ Polymer
Applications: Aerospace engine, automotive powertrain, and industrial system
LMPAEK™ is a molecularly modified PAEK (polyaryletherketone) incorporating extended polymer chains, delivering unique thermal stability, enhanced mechanical strength and superior chemical resistance, while achieving lightweight properties ideal for high-temperature applications such as aerospace engines and automotive powertrains.
The material maintains excellent mechanical performance at continuous operating temperatures up to 250°C, ensuring reliable
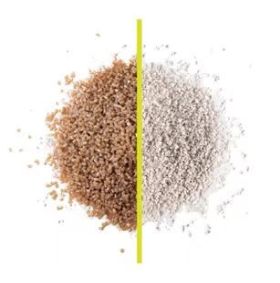
functionality even in corrosive or abrasive environments. Furthermore, its exceptional durability and degradation resistance significantly extend product lifecycles, reduce maintenance requirements and material waste, thereby enabling sustainable eco-friendly solutions.
∎ Arkema
Technology: Bio-based Rilsan® PA11
Applications: Hydrogen-powered vehicle
Arkema’s bio-based Rilsan® PA11 integrates exceptional low-temperature resistance, hydrogen compatibility, processability, and lightweight properties. Capable of withstanding frequent hydrogen charging/discharging cycles, it effectively reduces maintenance costs and is specifically designed for Type IV hydrogen storage cylinder liners in hydrogen-powered vehicles.
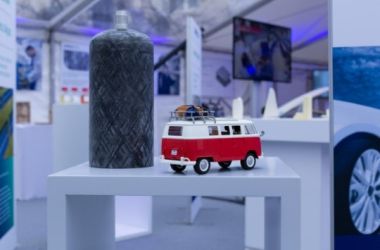
Rilsan® PA11 fully complies with GB/T 42610-2023 material standards. It provides lightweight solutions with high hydrogen storage density and durability for Type IV cylinder liners, while supporting multiple processing techniques including rotomoulding, extrusion, blow molding, injection moulding and stable welding processes. Derived 100% from renewable castor seeds, Rilsan® PA11 achieves dual carbon footprint reduction at both material and energy levels, enabling more sustainable development.
∎ Shenzhen WOTE Advanced Material
Technology: DuraKraft™ PEEK
Applications: Humanoid robotic, Low-altitude aircraft, automotive systems
Engineered with a density of 1.3g/cm³, WOTE DuraKraft™ PEEK delivers reduction in robotic arm load energy consumption versus conventional engineering plastics. In continuous gripping tests of robotic arms, DuraKraft™ PEEK gears achieve a service life of 2 million cycles, far exceeding those of conventional nylon and metal components.
Furthermore, the material maintains mechanical properties without degradation at 260°C, effectively eliminating deformation risks caused by motor heat generation in traditional plastics.
∎ KUMHO-SUNNY
Technology: Blade Plastic for Thin Walled Design
Applications: Low-altitude economy
KUMHO-SUNNY has launched its Thin-Wall Optimized Plastics, which demonstrate significant advantages in surface aesthetics, rigidity-toughness balance and warpage resistance compared to mainstream reinforced plastics.
The material exhibits exceptional dimensional stability with minimum warpage tendencies. Its premium look is on par with virgin-grade resins while significantly outperforming other reinforced products; high modulus (3,500-5,500 MPa) matches fiber-reinforced composites; the material also offers customizable toughness grades with impact strength up to 30 kJ/m².
High-toughness lightweighting
“Vibration damping” is emerging as a critical performance metric for automotive components and athletic footwear, not only directly impacting user safety protection and comfort experience but also representing a pivotal frontier in material innovation. Enhanced elastomer toughness achieves two objectives: weight reduction and vibration damping.
∎ Dow
Technology: ENGAGE™ 11000T Polyolefin Elastomer
Applications: Automotive interior/exterior trim, cable system, footwear
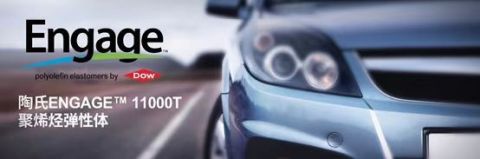
The new-generation ENGAGE™ 11000T series polyolefin elastomer materials exhibit lower glass transition temperatures alongside elevated melting and crystallization temperatures. This delivers efficient impact resistance, optimized toughness-rigidity balance and reduced linear thermal expansion coefficient with enhanced dimensional stability at elevated temperatures for modified polymers. The balanced toughening and flow properties further improve injection molding process efficiency.
Providing robust mechanical performance and superior resilience for automotive interiors/exteriors, cable systems and footwear applications, this material effectively addresses vehicular safety requirements while achieving lightweight toughening and metal substitution objectives.
Technology: Nylon 12 Elastomer (PEBA)
Applications: Footwear, Sports equipment, Industrial transportation
Wanhua Chemical’s Nylon 12 Elastomer (PEBA) employs fully self-developed technology, establishing a complete industrial chain from butadiene to dodecalactam and ultimately polyamide 12 elastomer. This material features ultra-low density (as low as 1.01 g/cm³). After foaming, it maintains high resilience while achieving a minimum density below 0.07 g/cm³, coupled with low water absorption, dimensional stability and easy processability. These performance advantages meet application requirements in footwear manufacturing, sports equipment and industrial transportation.
CHINAPLAS 2025
Notably, most participating companies will have presence at CHINAPLAS 2025 where more innovations will be showcased on site. Readers are welcome to visit CHINAPLAS 2025 to explore more.