Covestro will make its maiden appearance at International Suppliers Fair (IZB) 2016 with a focus on applications in the automotive interior.
Car buyers increasingly want a personalized vehicle interior with a premium feel and appealing design. On the other hand, the automotive industry wants to be able to manufacture components as cost-effectively as possible with high productivity.
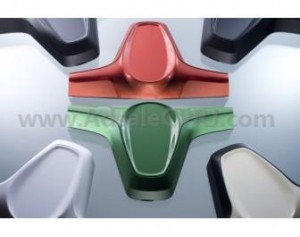
At the show, Covestro will be showing examples of its innovations, for example, the DirectCoating/DirectSkinning technology that combines design and efficiency.
The latest development is a steering wheel cover fabricated by the DirectCoating method. It illustrates a number of options that polyurethane (PU) coatings offer for designing component surfaces, including metallic effects and fine-grain textures with sharp transitions between matte and glossy areas.
With this two-stage process, coated components with any number of different designs can be produced economically and efficiently, according to Covestro.
Another option for the low-cost production of decorative interior parts is an injection molding process with dynamic temperature control, which is combined with physical foaming.
By combing both processes, components with reduced weight and superior surface quality can be manufactured. This technology was used to fabricate glove compartment covers made from Bayblend, Covestro’s blend of polycarbonate (PC) and acrylonitrile butadiene styrene (ABS). The surface features both high-gloss and textured regions. Manufacturers can also dispense with a separate coating step.
The company is also presenting a broad range of film products for automotive interiors at IZB. One key topic is matte films with scratch-resistant coatings that can be formed three-dimensionally. The product line is further enhanced by anti-glare films for integrated automotive displays.
IZB 2016 will take place in Wolfsburg, Germany from October 18-20.
Source : China Plastic & Rubber Journal